Machining
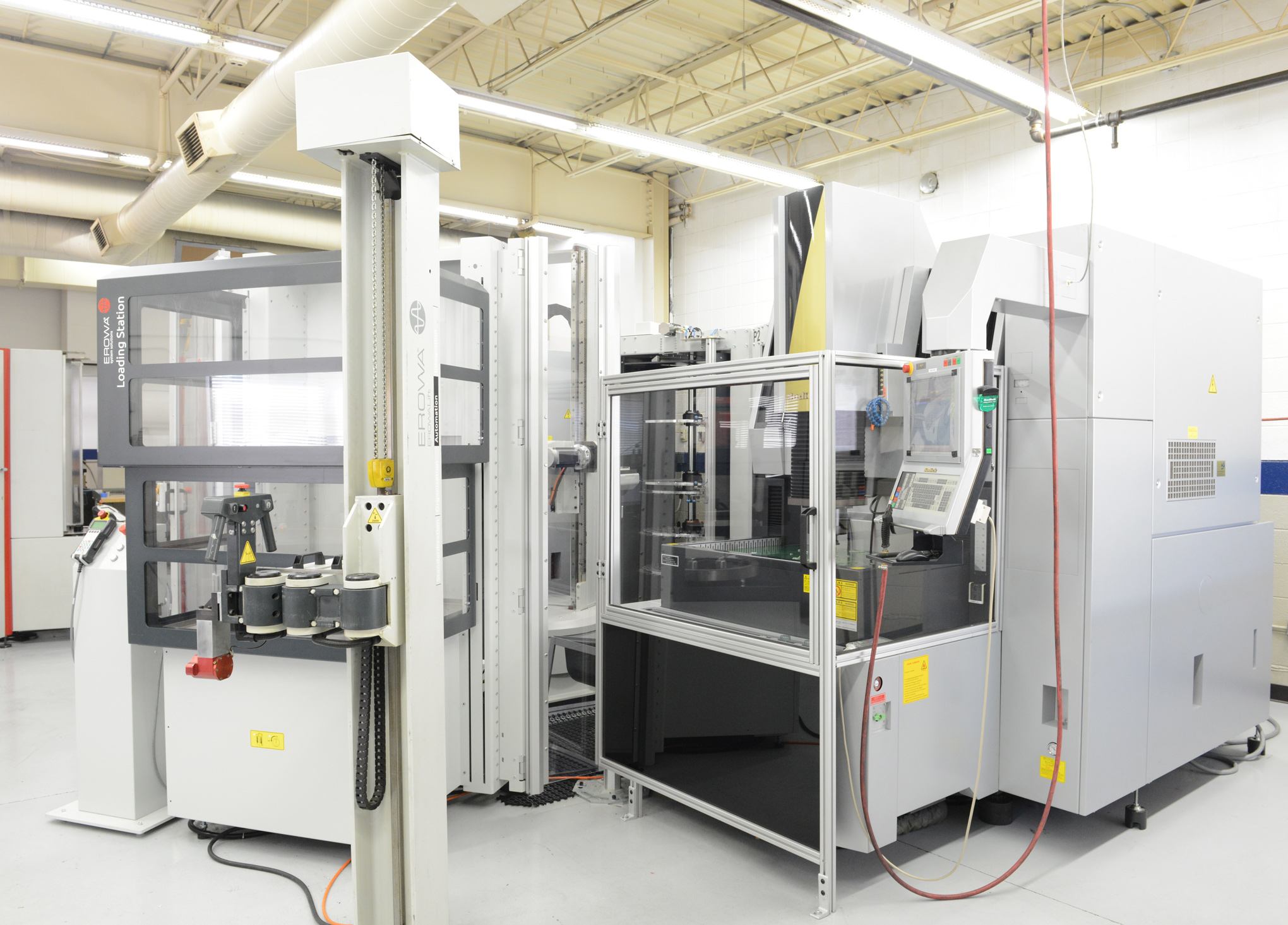
Adapting to the changing demands of advanced manufacturing is one of our greatest strengths.
Working smarter has proven to be a key part of our success. Our fully automated technology system uses Erowa robotics to create a more flexible manufacturing process within our machining department, and we operate an efficient “lights-out” operation.
Industrial Molds’ in-house machining department manufactures high-quality precision tool parts and components, with a team of experienced machine programmers and skilled operators who are equipped to handle any job. We are driven by systems and data, constantly striving to improve our machines’ workflow by minimizing downtime and maximizing throughput.
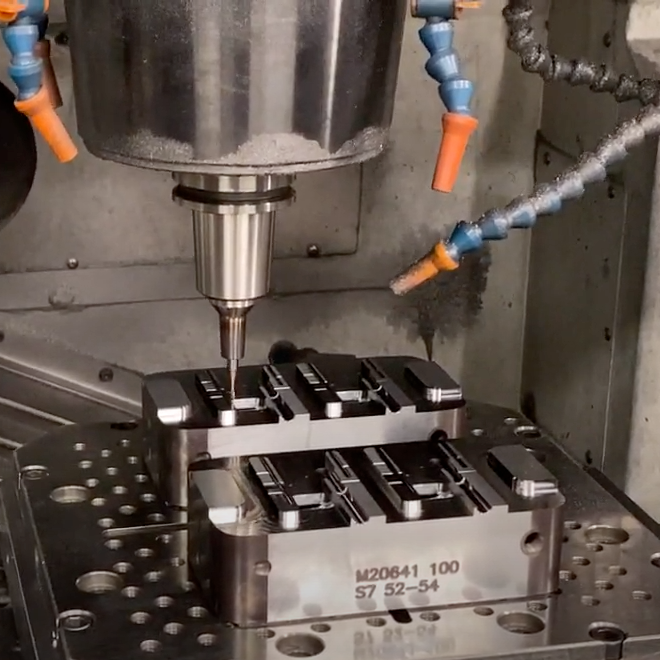
Our HSM department is populated by experienced programmers and operators, all focused on quality as a top priority. We utilize Shrink-Fit Tooling for increased
accuracy, and Erowa automation allows for repeatable “lights-out” runs. We program with PowerMill for smooth accurate tool-paths, and Blum and Renishaw probes are used in machine quality checks. This premium tooling guarantees optimum tool life and surface finishes.
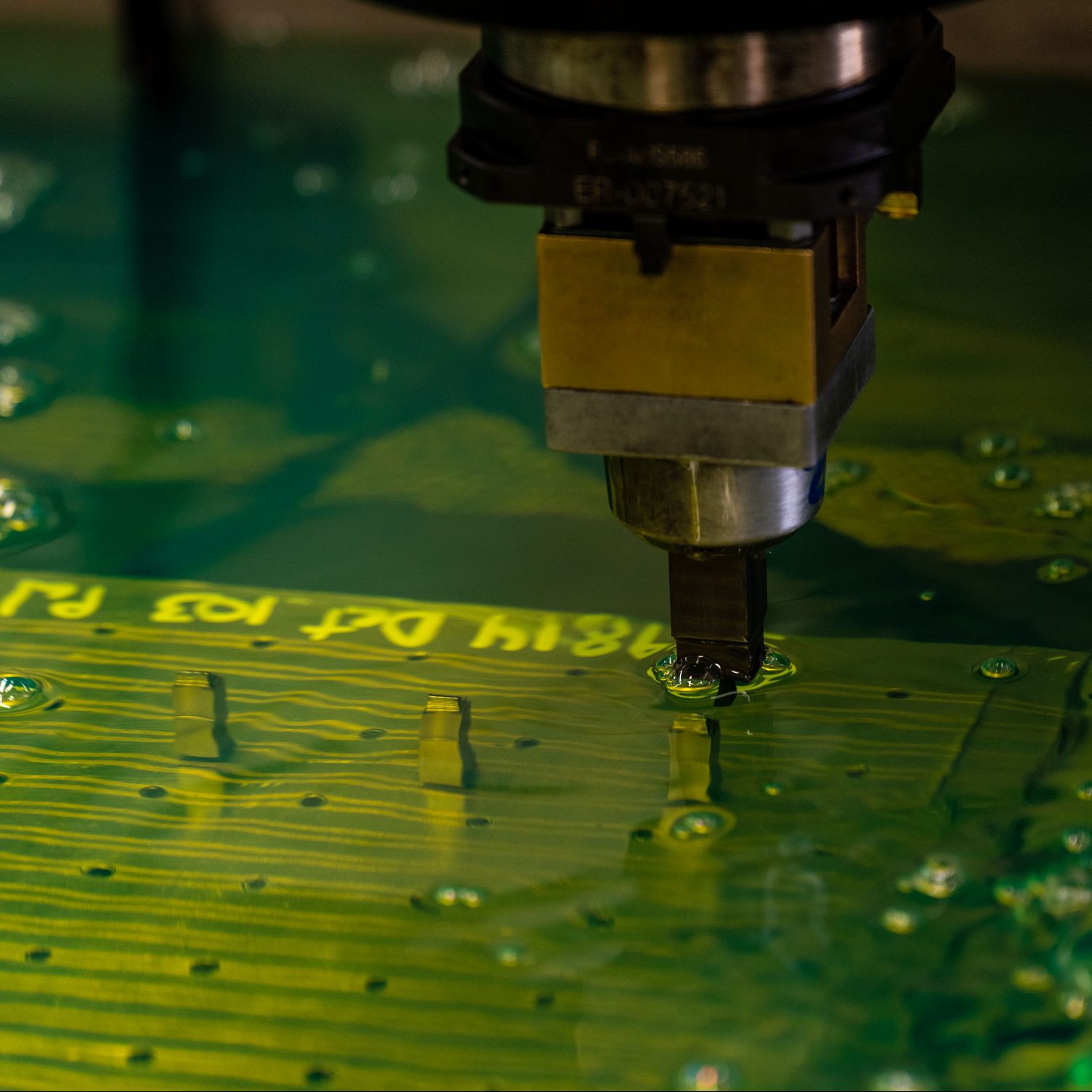
Our Sinker EDM department at Industrial Molds is equipped with fully automated Sodick AG60 sinkers with linear guides, which provide increased accuracy, speed, and finish. The technology used reduces the number of electrodes needed, resulting in reduced costs for our customers. Tight tolerances are achieved through the repeatability of our fixturing. Utilizing all axes in standard and special burns creates intricate details that standard machining cannot achieve. We generate power settings specific to each electrode in order to have complete control over roughing and finishing conditions, which is key when the surface finish of the mold cavity is critical.
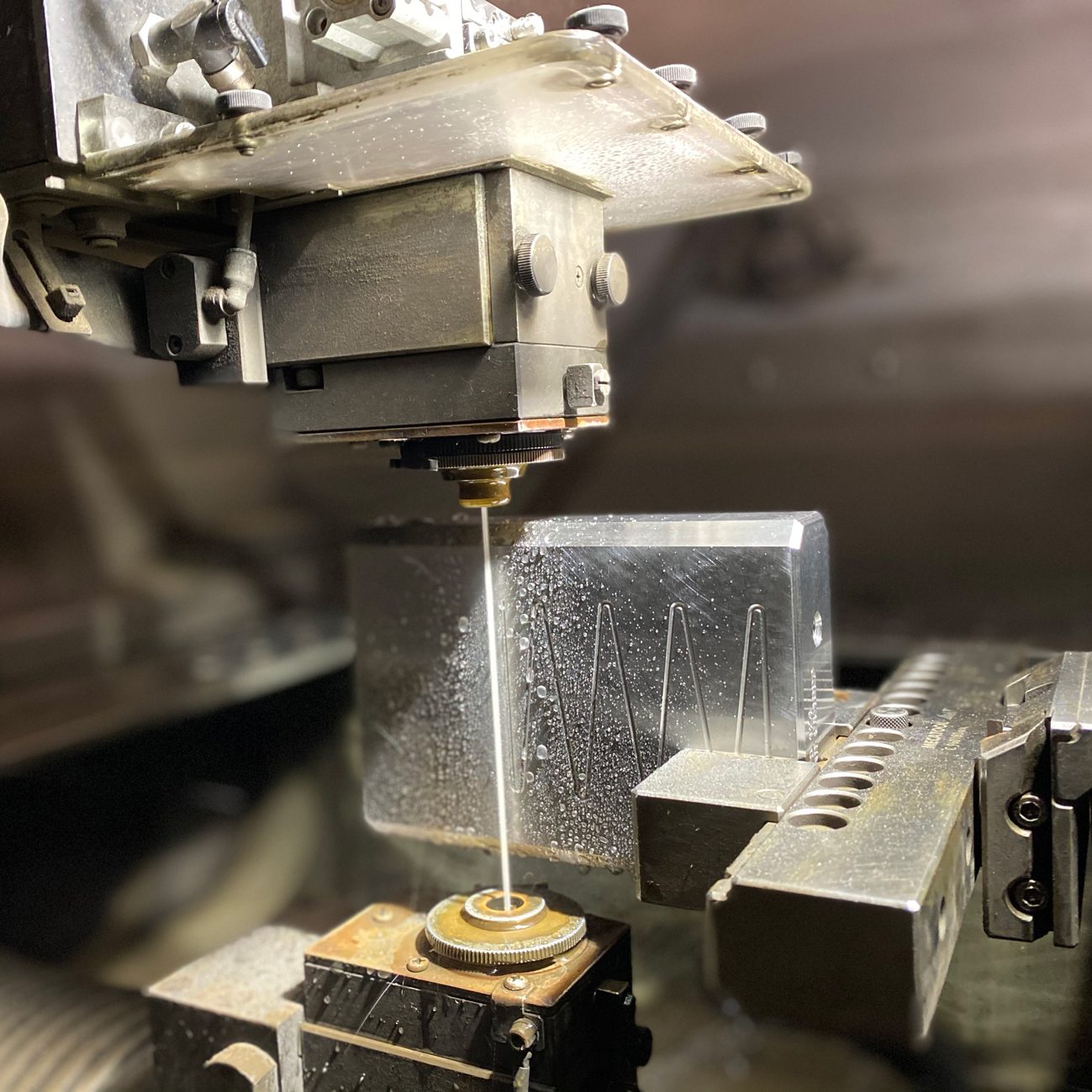
Our Wire EDM department features Makino U.6. H.E.A.T. machines using .010" brass wire, along with Makino U32J which puts .008" wire to use.These machines have the capabilities of burning a wide range of ferrous and non ferrous materials at varying thicknesses and sizes all while using the most efficient cut technology packs. Programming is done using the latest version of Esprit software that makes difficult 4-axis cuts seem effortless.
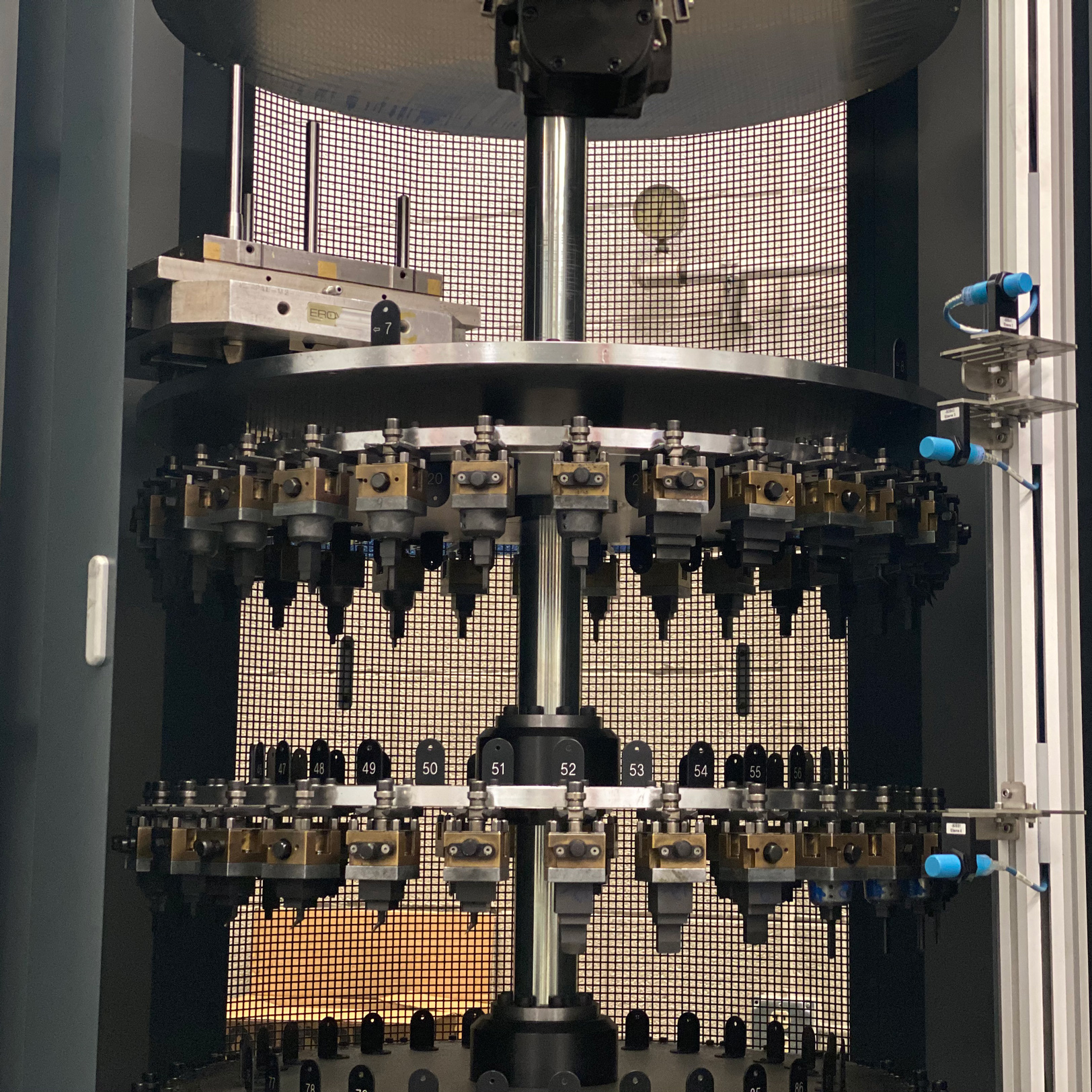
Our Carbon department machines electrodes in house, using dual 5 axis Micron machines. For speed, accuracy, and efficiency, the Carbon cell is centered around Erowa robotics using an automated carousel, allowing for continuous 24/7 manufacturing.
Case Study:
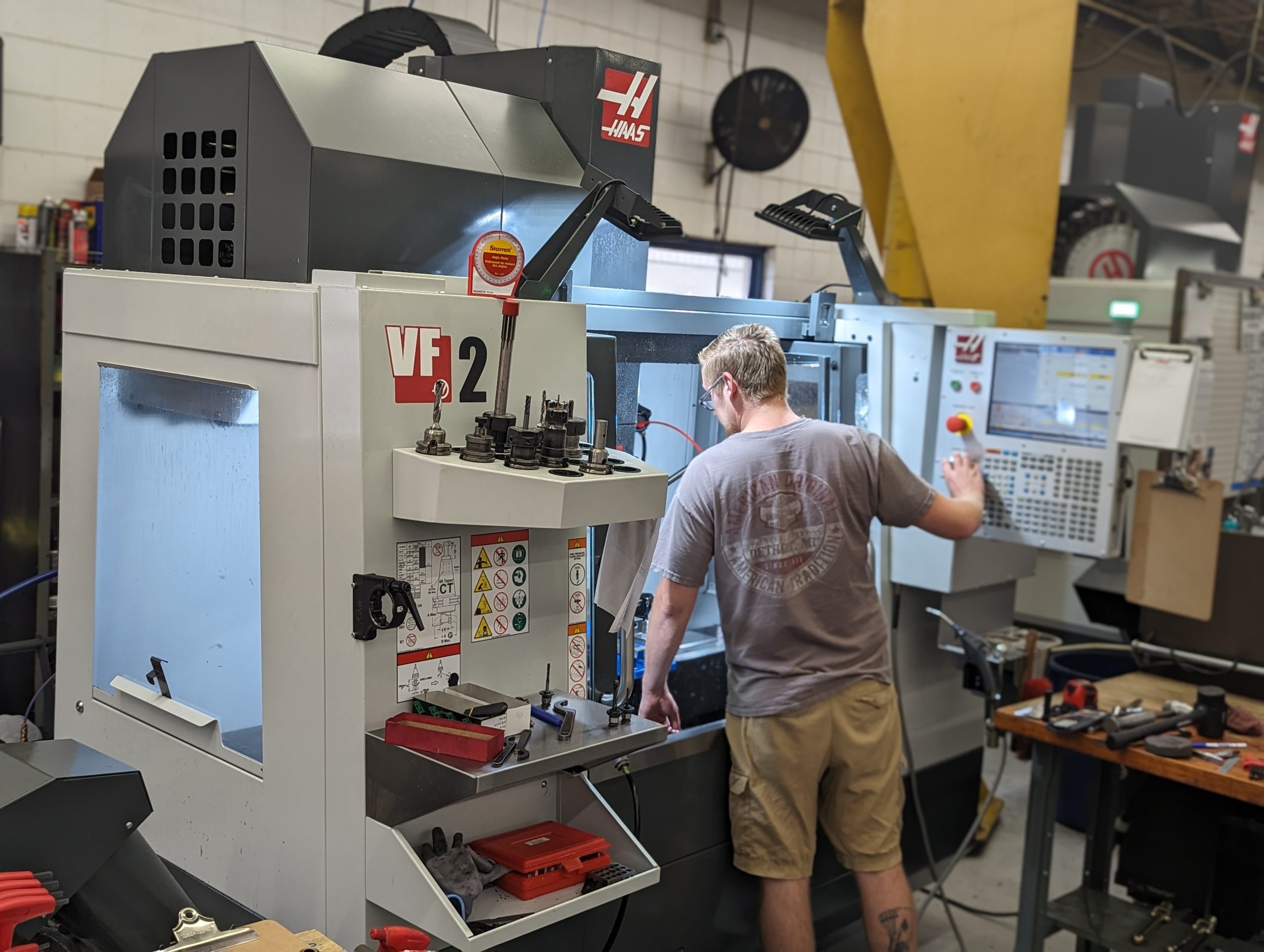
Using the Power of Focus to Increase Throughput and Impact the Bottom Line
Tooling Questions?
Ask a tooling expert
Equipment List
View Equipment List
We're ready to be Your Manufacturing Partner
Contact Us